As with many things produced in Italy, there is a level of craftsmanship and tradition with Murano glassware. Named after the Venetian island on which it is produced, Murano is suggested to have become the location for glassware production because of its isolated island location. The location was ideal because it offered protection to the city of Venice from possible fires due to the high-degree furnaces used in production. The process used today is very much as it was in the early days of glass production on Murano, let’s take a closer look.
A Long History
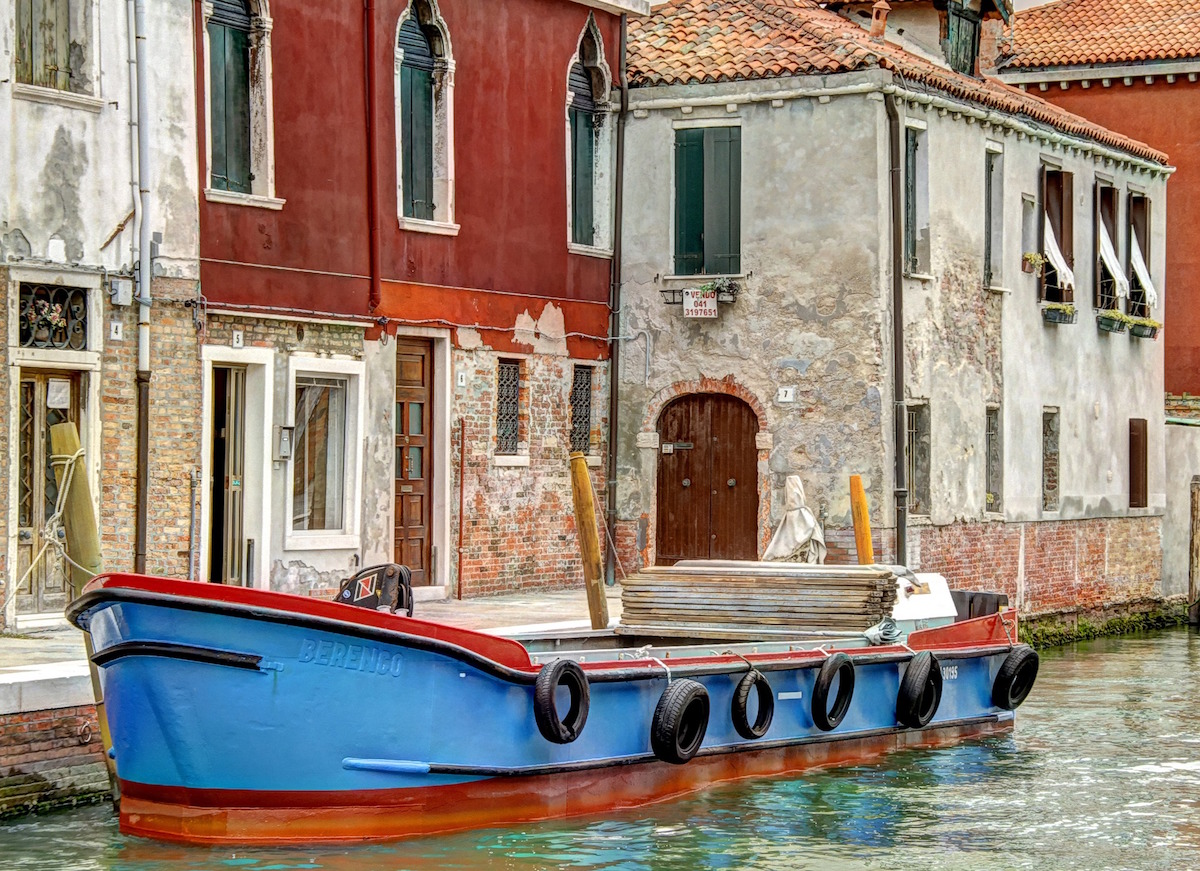
Glass production in Murano dates back hundreds of years, though in the 1960s archaeologists located what is believed to be one of the first glass furnaces on a Venetian island. While the furnace was found on the island of Torcello, it demonstrates the long history that Venice has had with glass production. In time, the Venetian authorities worked hard to protect the glass industry as well as its secrets.
While the glass reached a pinnacle of its early success in the 15th and 16th centuries, it began to fall into a decline in the 18th century for a number of reasons including the occupation of the area by other countries. Once Venice became part of Italy there was renewed interest in the glass of Murano and when Venice celebrated its biennial at the end of the 19th century this renewed interest grew. As we entered the 20th century, part of the increase in interest had to do with an appreciation for the traditional methods of glass making.
Glass Blowing
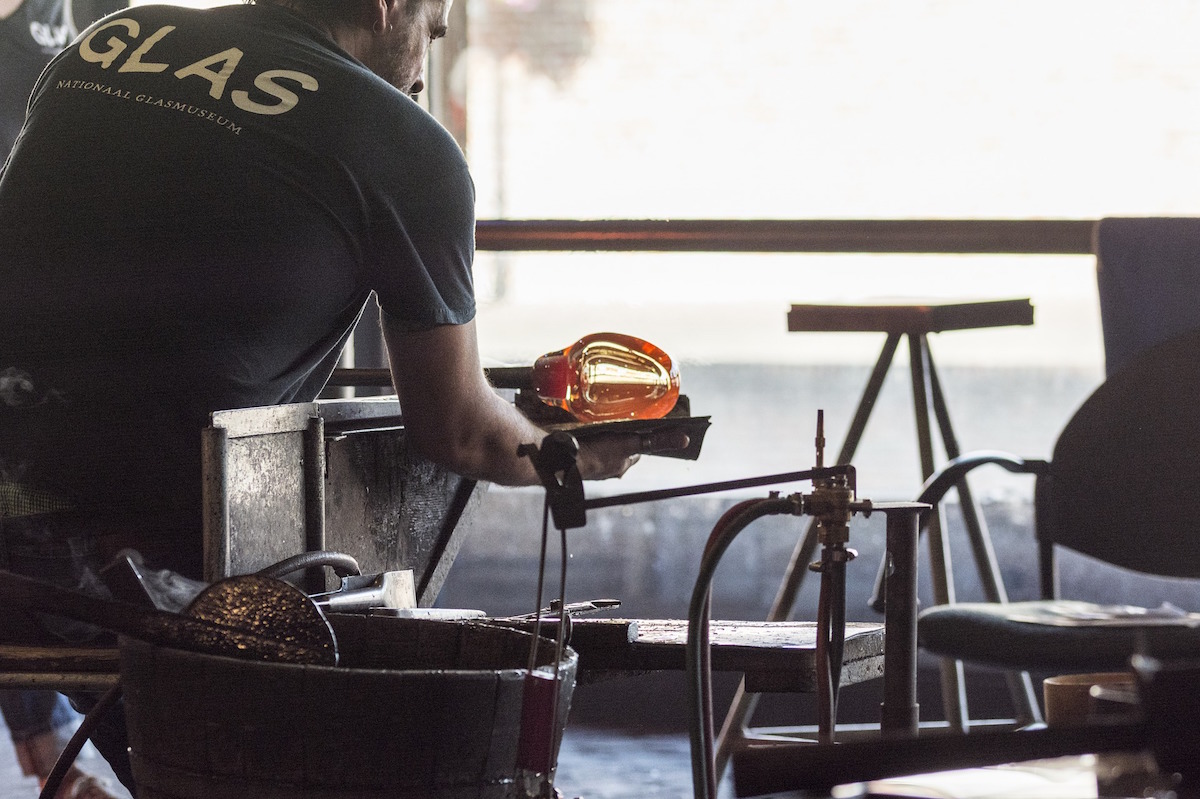
The first step in the process of creating these beautiful pieces is that the maestro (the glass blower) begins to work on the red-hot glass by using a rotation technique and employs tools to mold the glass. Then he proceeds to blow into the blowpipe to which the mass of glass is connected. This inflates and allows him to shape the glass, continuing the rotation technique between blows. In this example, we’re making a vase.
Adornments
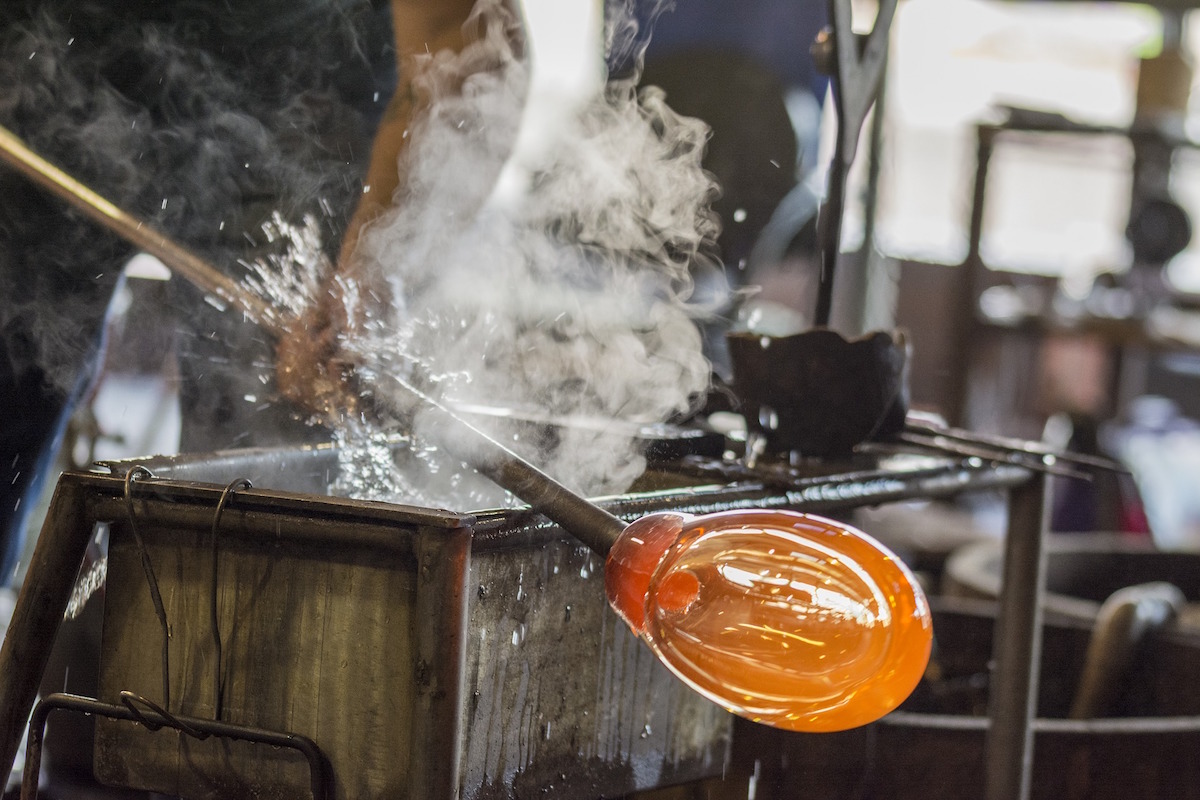
In this stage of production, the maestro will add the adornments which define Murano glass. One such adornment is gold leaf. He’ll roll the vase in gold leaf and place it back into the furnace until the leaf is fused with the glass. From there, he’ll pull it out and allow all the excess glass to drip off. At this point, he’ll roll the vase in pieces of marine glass and continue the rotation technique in a very precise and slow manner. This will allow him to adjust the thickness of the vase walls. He’ll continue to blow and will then add in the use of tools such as pliers to form the piece as desired. This is all done while maintaining a temperature for the glass in excess of 1,400 degrees Fahrenheit.
The Transfer
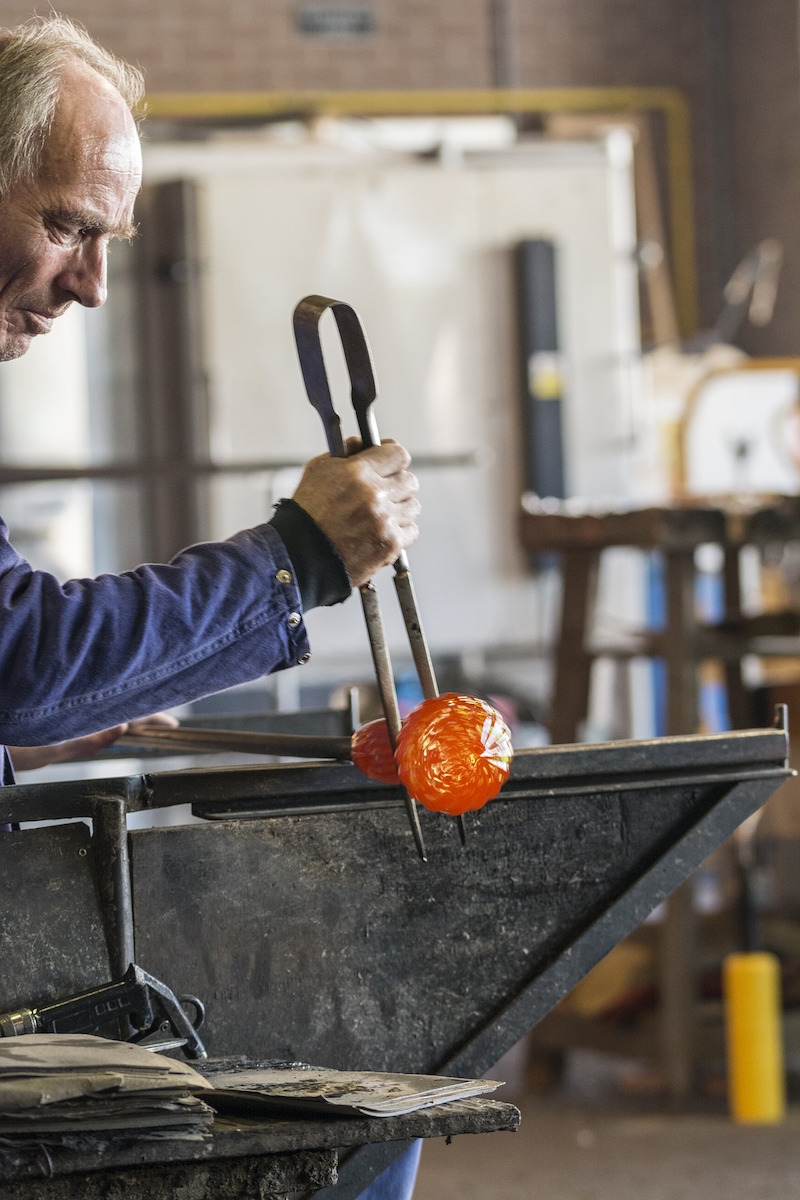
During this slow, methodical process, the vase is transferred to another blowpipe to work on the top portion. The rotation continues as does the use of additional tools such as pliers and scissors, allowing the maestro to mold the vase into a perfect form. Once the form is achieved, the cooling process can begin. The first step in the cooling process is to leave the vase in a furnace overnight to slowly allow its temperature to decrease to avoid any damage.
Beyond a Vase
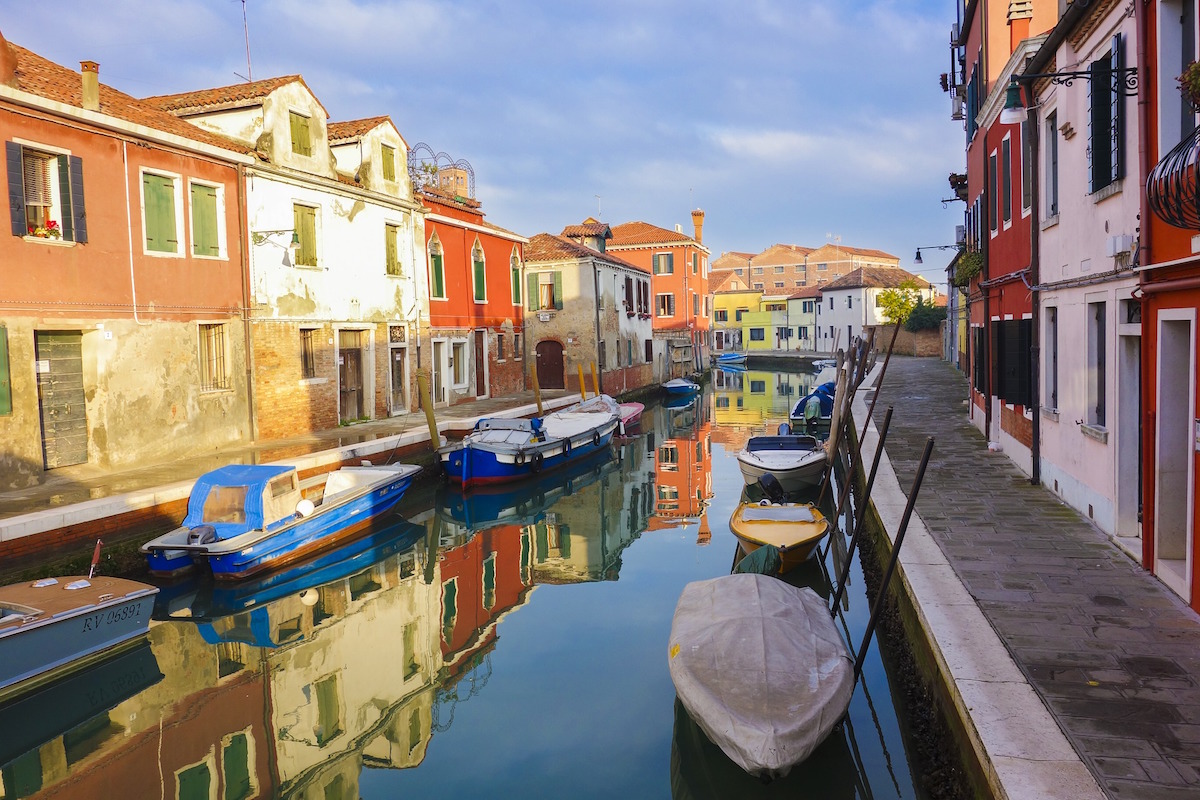
There are many other items of fine glassware produced in Murano. While some criticism has come up over the years because of the tourist industry and cheap reproductions, the true artists in Murano continue to create vases, stemware, dishes, sculptures, chandeliers, and more. In doing so, they’re keeping the history and tradition of Murano glass making alive and well.
Should you decide to visit Murano when you’re in Italy, a tour and glass blowing demonstration is a must. We’d also recommend a water taxi ride to and from the island as well as a stop in Burano, the neighboring island, for a lovely stroll and maybe a delicious meal. If you’re looking for the best accommodations for your trip, try our picks for luxury hotels in Italy. There is even a good recommendation for Venice on the list.
So, tell us, do you own any original Murano glass?